Simulateur de retournement
(voiture tonneau)
Les accidents de la route constituent une préoccupation majeure dans le monde entier, entraînant souvent des conséquences dramatiques. Parmi les différents types d’accidents, le retournement de véhicule représente un scénario particulièrement dangereux. Afin de mieux comprendre les mécanismes en jeu et de sensibiliser les passagers de voitures, et plus particulièrement les jeunes, à porter leur ceinture de sécurité à l’avant et à l’arrière, l’utilisation de simulateur de retournement, communément appelé « voiture tonneau », est devenue une pratique courante de la sécurité routière.
Nous présentons ici une étude réalisée par l’équipe de XADICE ENGINEERING sur un simulateur de retournement :
- définition des contraintes et fonctions de l’équipement,
- recherche de concepts permettant de remplir au mieux les besoins,
- définition d’une architecture structurelle,
- prédimensionnement mécanique,
- dimensionnement des équipements électromécaniques,
- sélection de composants standards,
- conception mécanique,
- modélisation géométrique 3D,
- étude électrique,
- calcul de structures et simulations mécaniques, et enfin
- documentation.
Architecture du simulateur
Le simulateur de tournement est un équipement autonome constitué d’une remorque supportant un châssis mobile rotatif sur lequel est installée une cellule de véhicule de tourisme. Bien que dépouillée d’un certain nombre de composants devenus inutiles – moteur, réservoir, essieux – la caisse du véhicule conserve l’aspect extérieur et tous les équipements intérieurs d’un véhicule classique – sièges, volant, tableau de bord – afin de rendre l’expérience aux utilisateurs la plus réaliste possible.
L’architecture structurelle retenue est constituée d’un châssis de remorque routière qui supporte tous les équipements nécessaires aux déplacements vers les différents sites d’exploitation.
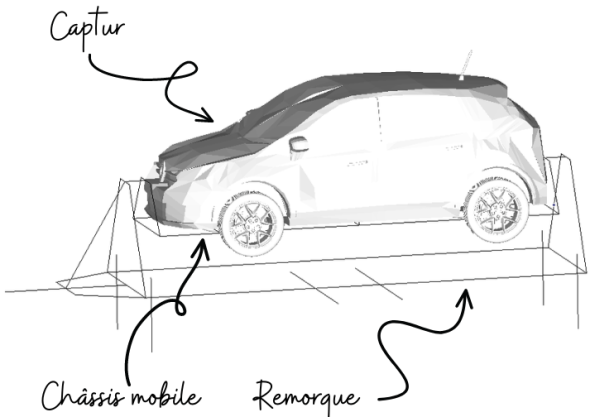
Un châssis mobile (rotatif) supportant la cellule du véhicule vient s’interfacer avec la remorque et permet une rotation motorisée et contrôlée (vitesse et sens de rotation).
La remorque est déplacée en étant tractée par un véhicule utilitaire en empruntant les voies routières sans contrainte particulière. Cette remorque comporte toutes les dispositions d’homologation pour circuler sur les routes françaises : essieux freinés, signalisation, plaque minéralogique, feux de route, etc.
Le châssis mobile est monté sur deux articulations aux extrémités et une transmission par chaîne permet à un motoréducteur de contrôler la rotation de l’ensemble mobile.
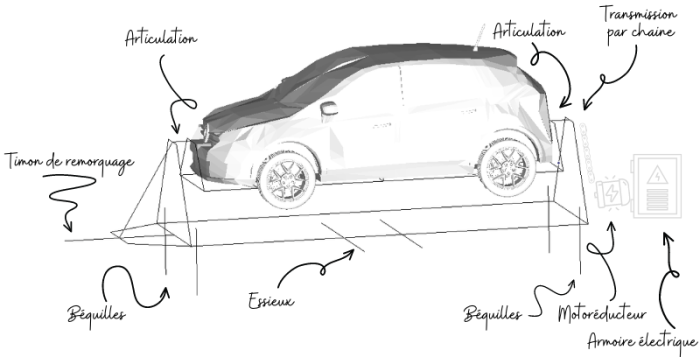
Prédimensionnement
Une attention particulière a été portée à la minimisation du poids de l’ensemble pour offrir une souplesse de configuration de déplacement et éviter de rentrer dans des catégories de véhicules nécessitant des dispositions particulières (permis).
La phase de prédimensionnement a permis d’itérer rapidement afin d’optimiser l’échantillonnage des poutres des châssis et d’obtenir des performances préliminaires satisfaisantes avec un bon compromis performance / masse.
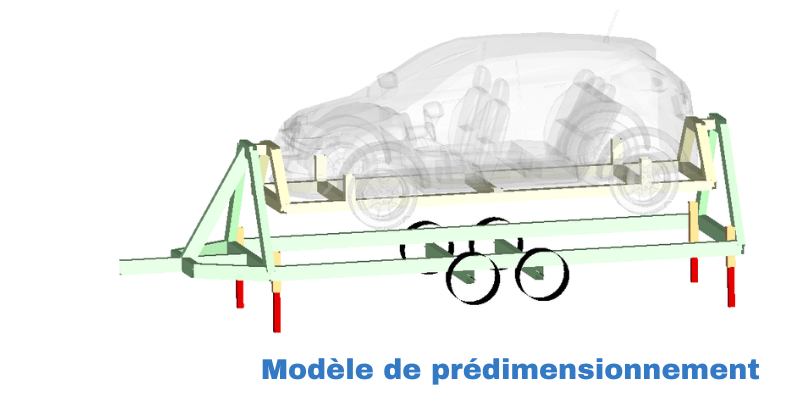
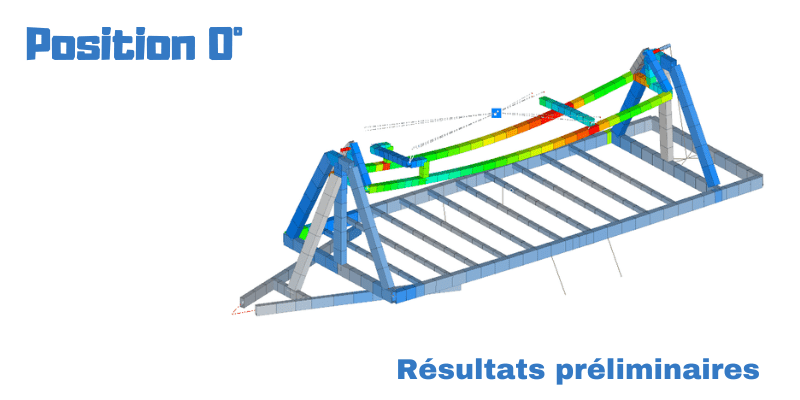
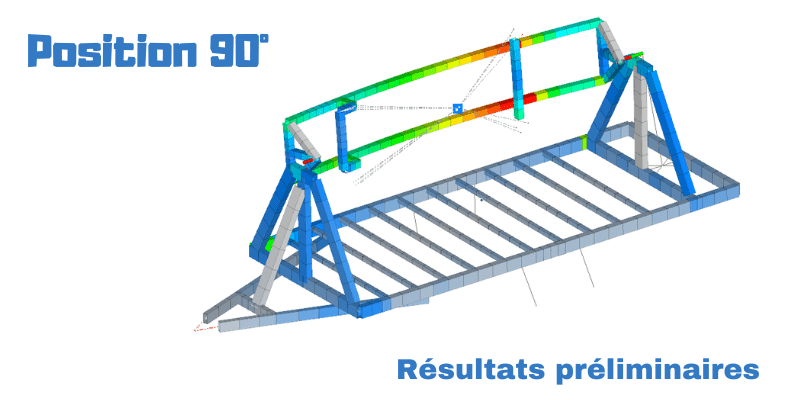
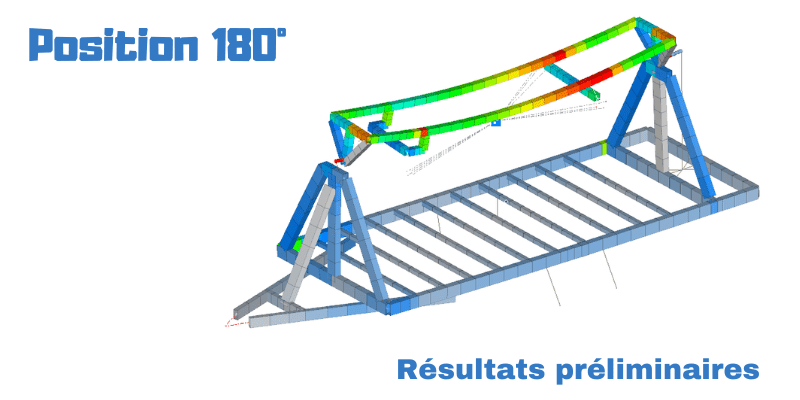
Validation du dimensionnement
La phase de validation des performances et d’optimisation de la masse a été réalisée sur une modélisation détaillée de l’ensemble du simulateur pour améliorer la résolution et la précision des résultats. Le modèle éléments finis, développé avec la suite logicielle FEMAP/NX-NASTRAN, comporte des éléments volumiques, coques (majoritairement), poutres, masses ponctuelles et corps rigides. Les différentes liaisons mécaniques ont été intégrées pour représenter le plus fidèlement possible le comportement du simulateur. La cellule du véhicule est restée modélisée grossièrement pour uniquement considérer sa masse et son inertie puisque sa tenue mécanique n’a pas nécessité d’analyse particulière.
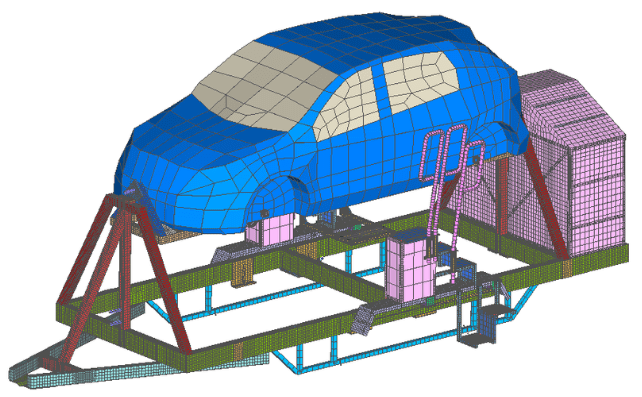
L’étude s’est appuyée sur les normes suivantes :
- NF EN 13814 « Machines et structures pour fêtes foraines et parcs d’attraction – Sécurité »
- NF EN 12195 – Dispositifs d’arrimage des charges à bord des véhicules routiers
- EUROCODE 0 – EN 1990 « Base de calcul de structure »
- EUROCODE 1 – EN 1991 « Action sur les structures »
- EUROCODE 3 – EN 1993 « Calcul des structures en acier »
- EUROCODE 9 – EN 1999 « Calcul des structures en aluminium »
Cette modélisation a été employée pour représenter le comportement mécanique du simulateur sous diverses conditions :
Phase de circulation : accélération et freinage du véhicule tracteur, effets de la force centrifuge en virages, effets de l’air liés à la vitesse de circulation et du vent transverse.
Phase de montée/descente des passagers : Efforts générés par les charges permanentes (masses soumises aux effets de la gravité) et des charges de montée / descentes des passagers.
Phase de simulation : efforts générés par les charges permanentes, charges dynamiques (inertie), effet de balourd lié à l’excentrement du centre de gravité de l’ensemble incluant les passagers selon différentes positions angulaires du berceau rotatif et impact du vent maximum en utilisation.
Phase de stockage : charges climatiques sévères (vent).
Les calculs sont réalisés avec le solveur NX-NASTRAN selon différentes configurations en statique (SOL 101) et en dynamique (SOL 402). La rotation complète de l’ensemble châssis mobile + cellule de véhicule a été réalisée afin d’obtenir les niveaux de contraintes dans l’ensemble de la structure et les efforts/couples dans les différentes liaisons selon toutes les positions possibles.
L’analyse de résultats a permis d’identifier les zones de fortes sollicitations, les efforts dans les liaisons et aux appuis ainsi que les déplacements / déformations du simulateur.
Le dépouillement approfondi et les vérifications complémentaires ont été menées pour vérifier la tenue mécanique d’ensemble et de détails notamment la visserie et les soudures.
Ces analyses numériques ont permis de lever tous les risques et de s’assurer d’une bonne tenue mécanique du simulateur pour une exploitation pérenne et en toute sécurité tant pour les animateurs que pour les passagers.
Modélisation géométrique et mise en plans
L’étude a été finalisée par la mise en correspondance du modèle CAO 3D avec le modèle de calculs pour ainsi constituer la nomenclature de l’équipement et de réaliser les plans d’ensemble et de fabrication.
La documentation est complétée par la rédaction d’une notice d’utilisation et la réalisation d’un support de formation des opérateurs.
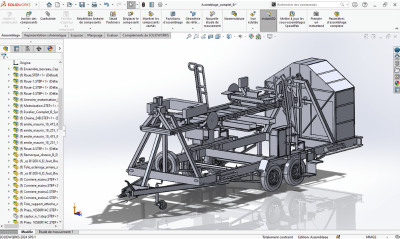
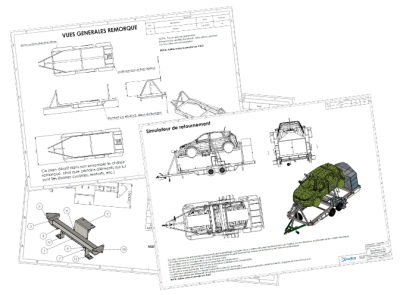
Réalisation et mise au point
La réalisation et l’intégration ont été menées à bien.
Des essais ont été réalisés pour s’assurer du respect des objectifs initiaux et des bonnes performances du simulateur même en conditions dégradées.
Les opérateurs du simulateur ont été formés à son utilisation pour une exploitation en toute sécurité.